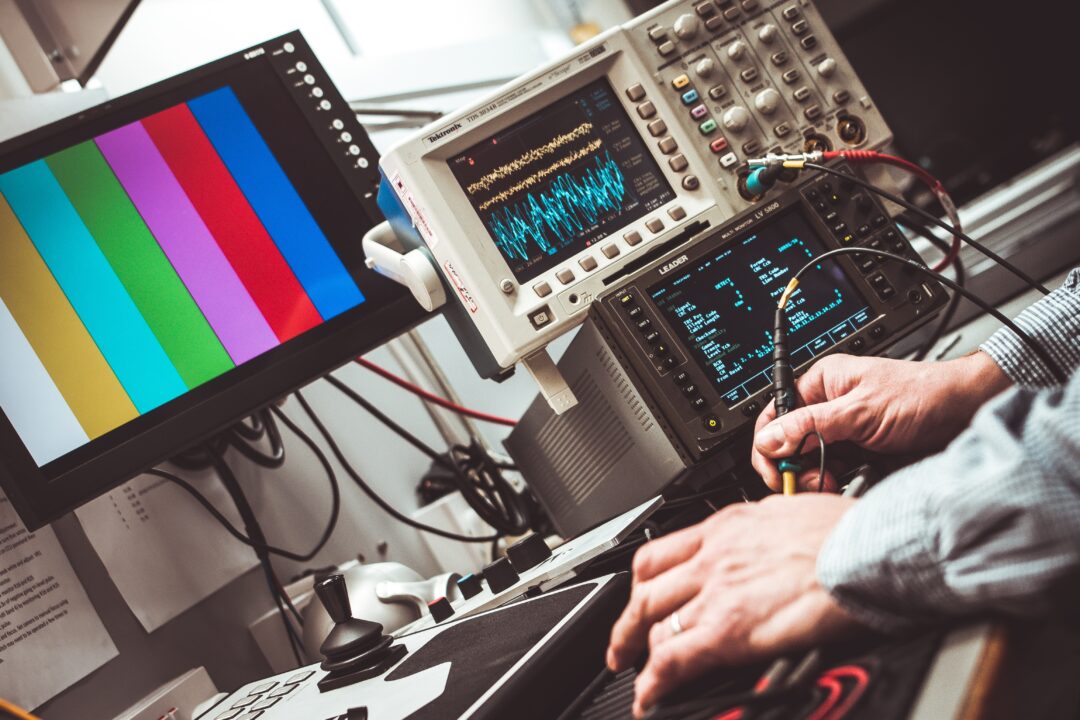
Octavic is a startup that develops a system that can help business from various industries to be more productive and reduce waste. The average monthly operating cost is wasted by 15% because many companies are not efficient and have many problems when it comes to wasting resources.
Octavic is based in Romania, Oradea and in Denmark, Copenhagen and develops I5.0 systems that helps companies and factories to save money on waste, taking care of wellbeing of the employees, environment, energy and many more.that is used by big companies from pharma and medical industry in order for them to grow productivity.
The product that Octavic team builds is called PET – Production Efficiency Tracker – a modular, distributed system with hardware and software components. More precisely is an integrated system that helps companies receive real-time information to be more productive in a simple and smart way. The system provides visual management in factories, which helps to improve prioritization and problem management.
solutions. The system not only monitors the processes but also the actions that were undertaken by whom in a simple way, noting the data – explains the representative of the startup.
- Stops / delays
- Good units produced
- Rejects or scrap, by typology
- Material requests via eKanban
- Process parameters
All data collected from production is used to plan production in real time taking into account the risk factors that may cause delayed deliveries (overall efficiency of the equipment, defect rate, history of shutdowns, maintenance, energy consumption profile, production staff or fixtures availabilityetc.),
Many businesses do not have a systematic way to improve their production, so they do not think about such systems.
Multinationals have a difficult decision-making process and it often takes too much approval to start an installation – say the two founders.
As for the customer profile, they claim that this system is built in such a way that it can be adapted, in the shortest time, to any industry. Adoption by shopfloor personnel is painless – anyone who is familiar with a smartphone will have no issue operating the Octavic tablet, and we measured that in an 8h work shift, an operator interacts with our tablets 3-4minutes – so it’s non-intrusive to their productive time.
How Octavic is monetized
We offer the system as a subscription-based solution, deployed either on-prem or in cloud. Being a subscription service, this means the risk for the customer is minimal, and we guarantee money-back should they choose to not use it anymore – it never happened to us, but we are confident to offer this option.
Even though the technology to achieve such solutions has been on the market for 20 years, many companies do not use such a solution or have various non-functional solutions. Octavic identified that the main problem is that even if there are different systems that solve an individual problem very well (planning, visualization, statistics, data acquisition) create many other problems (how to integrate them, do not correspond to different types of processes, are expensive, difficult to install, etc.) there is no complete and integrated solution, easy to install and cheap.
You can find more informations regarding Industry 5.0 and how can Octavic PTS can help your company grow – if you visit our https://industry50.com