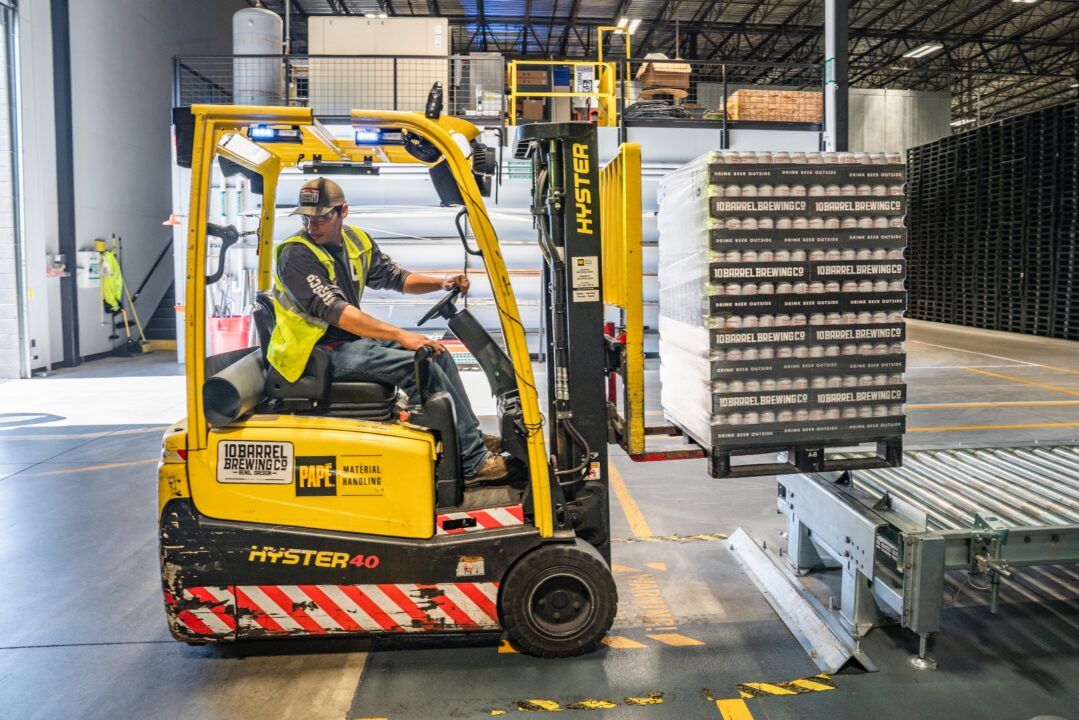
FIND OUT HOW CAN YOUR FACTORY REDUCE WASTE VIA OCTAVIC
Octavic built a unique, modular, distributed system that helps factories receive real-time information, by SMS and email for example, or on mobile, aggregated to the right granularity, so that it provides the right data infrastructure to become more productive in a smart and painless way. The system also ensures visual management in factories, which helps improve prioritization and issue management.
In addition to the visualization components, the system is able escalate problems hierarchically, collect data automatically and transmit that data to other digital business systems like ERP, WMS or BI solutions. The system not only monitors the processes but also the actions that were undertaken and by whom, in a simple way.
DO YOU WANT YOUR FACTORY TO BE MORE PRODUCTIVE? FIND OUT HOW:
To achieve this goal, the Octavic system can interface with production equipment to gather machine data and provides a simple guided workflow for shopfloor personnel to provide the much-needed human context.
The industrial equipment interface automatically collects machine data related to run times, stop times, delays, good units output, rejects or scrap by typology, material requests via eKanban, process parameters. The shopfloor staff then annotates or contextualizes the machine data, providing input such as stoppage reason for example.
All this data collected from the production floor is then further used to schedule production in real time, considering the risk factors that may cause delayed deliveries (overall efficiency of the equipment or OEE, defect rate, history of stoppages, maintenance metrics, energy consumption profile, production staff or fixtures availability, etc.). This helps factories achieve a systematic way to improve their production operations.
One factor that holds back digitalization in industry is the concern that adoption will be difficult for the personnel. The Octavic system is built so that it can be adapted, in the shortest time, to any industry. Adoption by shopfloor personnel is painless – anyone who is familiar with a smartphone will have no issue operating the Octavic tablet, and we measured that in an 8h wok shift, an operator interacts with our tablets 3- 4minutes – so it’s non-intrusive to their productive time.
The system is offered subscription-based, deployed either on-prem or in cloud. Being a subscription service, the risk for the customer is minimal, and the company guarantees money-back should the customer choose to not use the system anymore – it never happened to us, but we are confident to offer this option.
Even though the technology to achieve such solutions has been on the market for 20 years, many companies do not use such a solution to have various non-functional solutions. Octavic identified that the main problem is that even if there are different systems that solve an individual problem properly (like scheduling, visualization, analytics, data acquisition), they also create many other problems (how to integrate systems, some are industry-specific, some are not accessible as costs, difficult to install, etc.). And here is the unique proposition for Octavic – a turnkey, complete, complex but not complicated system, with painless adoption.
Octavic is a startup that develops a system that can help industrial manufacturers be more productive and reduce waste – both material and energetic. On average, up to 15% of operational man-machine costs are wasted due to delays, breakdowns and sub-optimal production scheduling.
Octavic is a company based in Oradea, RO with offices also in Copenhagen, DK that develops Industry 5.0 systems to help industrial manufacturers save money on waste, improve energy efficiency and gain predictability by optimal production scheduling. The system is adopted by multinationals in the pharma, tobacco, FMCG and building materials verticals, and not only.
You can find more information on Industry 5.0 and how Octavic can help your factory improve on our website https://industy50.com or https://octavic.io